Modelling and Simulation
From the smallest device to the largest system, each object is made up of heterogeneous parts, ant the coordination of these parts is essential for the success of the whole. Operating in such a context requires rapid decisions, in response to changes in market demands, environmental conditions, and business scenarii. Also, these decisions must be taken while minimising the risk of negative effects for the life cycle of the project, so as to ensure investment protection.
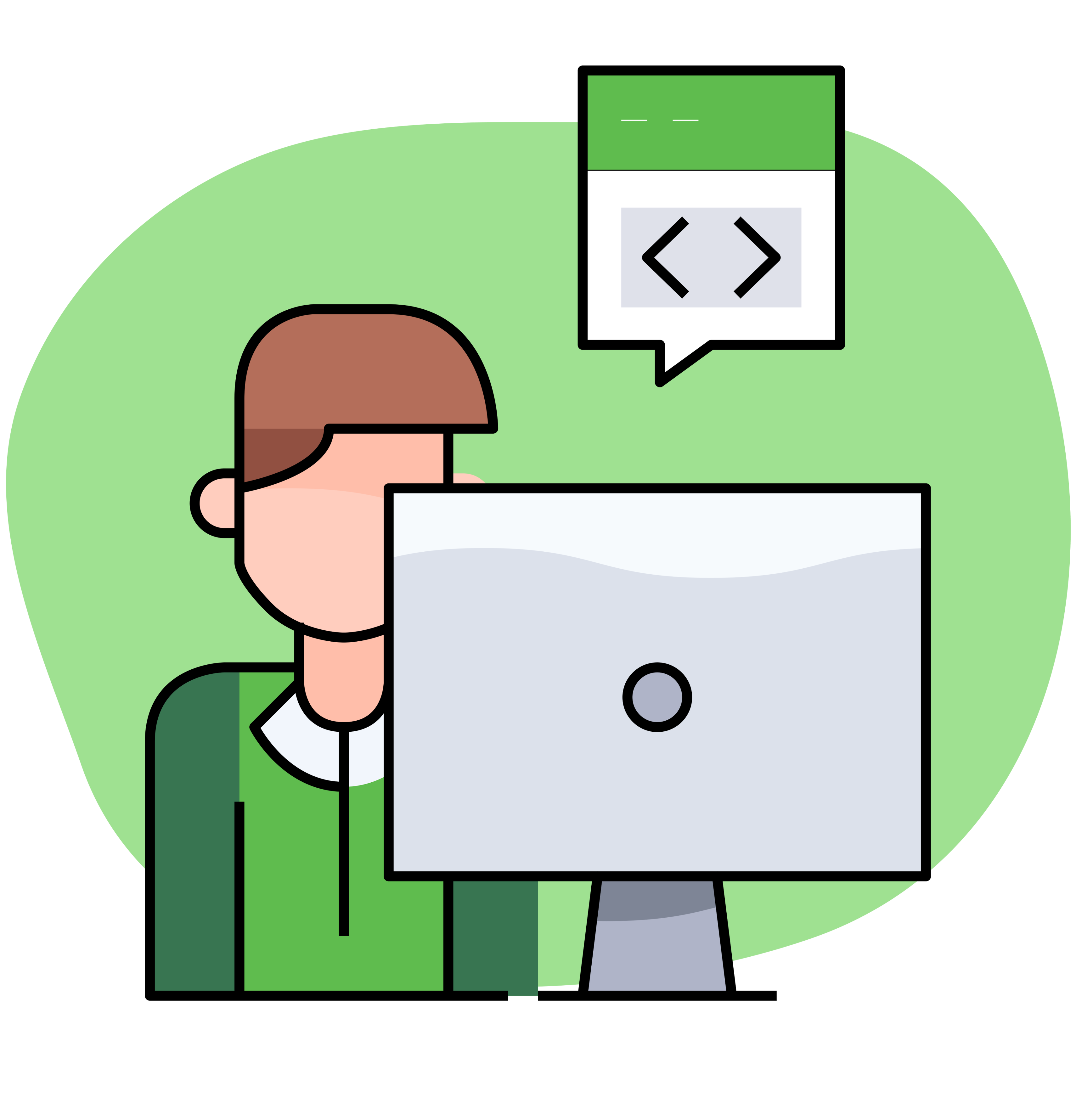
Modelling and simulation provide a knowledge domain, shared (in various declinations) by all the professionals involved in engineering activities and decision processes, at every stage of a project’s life cycle. This requires innovative tools, capable of managing knowledge with a single vision:
- multi-domain problems (mechanical, hydraulic, thermodynamic, electrical…), beause critical decisions often involve
several of them; - calable models, to adapt the degree of detail (i.e.,the complexity) of the solution to the available knowledge about the problem in the various phases of the project;
- models that are modular, reusable and adaptable throughout the life of the project (and even beyond…);
- completely customisable components, to respond promptly to the needs of the customer;
- synthetic description of control systems, for strategy verification, and of the test code for their implementation.
Our project workflow comprehends and addresses all these aspects, combining them according to the needs of the different operational phases.
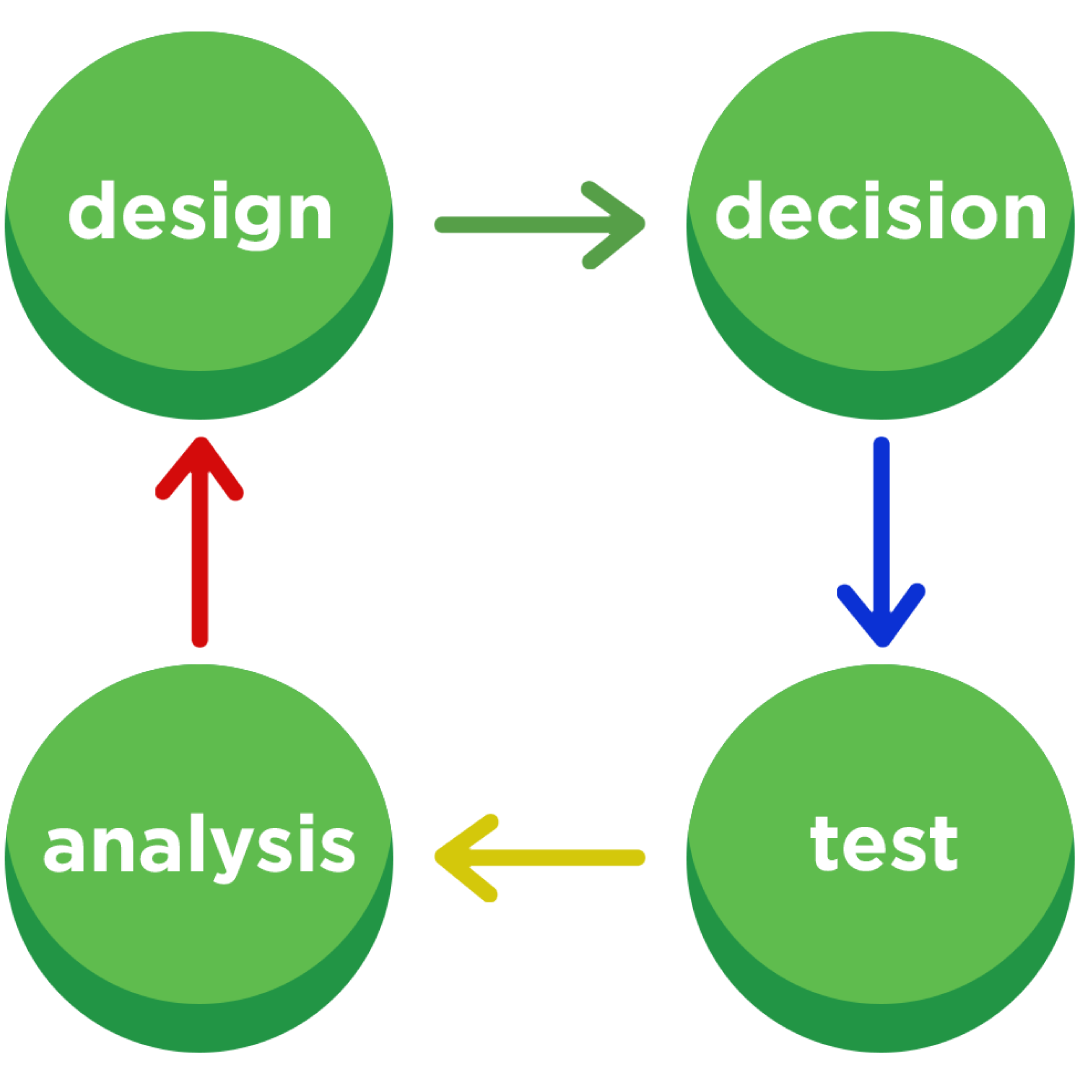
The consequent workflow is not linear, rather it is best represented by a cycle that repeats at each refinement phase, and in which the following phases alternate:
- project
- choice
- test
- analysis of the results
At each cycle, Modelling, Simulation and Virtualisation can be of fundamental help.
- For the project: modelling allows to evaluate multiple scenarii (market, operational, risk, failure …) while maintaining a unified vision of the whole;
- For the choice: the simulation of all scenariii, and their possible variants, allows to make choices that lead to a refinement of the overall performance of the system being designed, evaluating both the local and immediate effects of a solution and the more generalised and long-term ones;
- for the test: the set of choices made must be tested as a whole on different operational scenarii, and such testing must be repeatable so as to allow evaluating subsequent refinements; the virtualization of the physical system allows to carry out test campaigns that always start from well-defined conditions (therefore exactly repeatable), reduces the number of prototypes to be built, allows to perform potentially destructive tests (such as failure tests) that are difficult – if ever possible – to carry out with real prototypes;
- for analysis: the execution of tests on virtual models provides a quantity and a variety of data that can hardly be imagined with the tests carried out on real physical systems, bowing to both measurement costs and difficulty or impossibility of carrying out some types of measurement. The availability of a virtualised model, alongside (wherever possible) with prototypes, conversely allows for a more complete and generalised analysis of the effectiveness of the choices made.
The cyclical refinement process ends when the test analysis shows that the project objectives are met with the desired level of performance.
The next step in the project workflow normally involves the realisation of the found solution. This can have very diversified aspects, depending on the project context.
When the “system realisation” involves the implementation of solutions on control, data transmission and analysis systems, having the “digital twins” of the real physical system available allows to test more quickly and more extensively the implementation under question. Furthermore, the preliminary test phase can be carried out at the site where the implementation is being carried out, which can be very far from its final location.
Another very important aspect is that the virtualized system can be made available in advance with respect to the real one (think for example of an industrial plant). This allows to pre-check the compliance of the implemented system with the objectives and performance requirements, and if needed to carry out further refinement cycles without significantly affecting the project planning.
In the case of projects relating to the construction of production lines or industrial processes, the implementation phase is followed by the commissioning phase. The models and virtualisers used during the design phase can still be of help, in planning the tests and procedures to be performed during commissioning (especially those relating to scenarii that can stress the real system). These possibilities bring significant savings in terms of time and increase the safety level of the tests carried out.
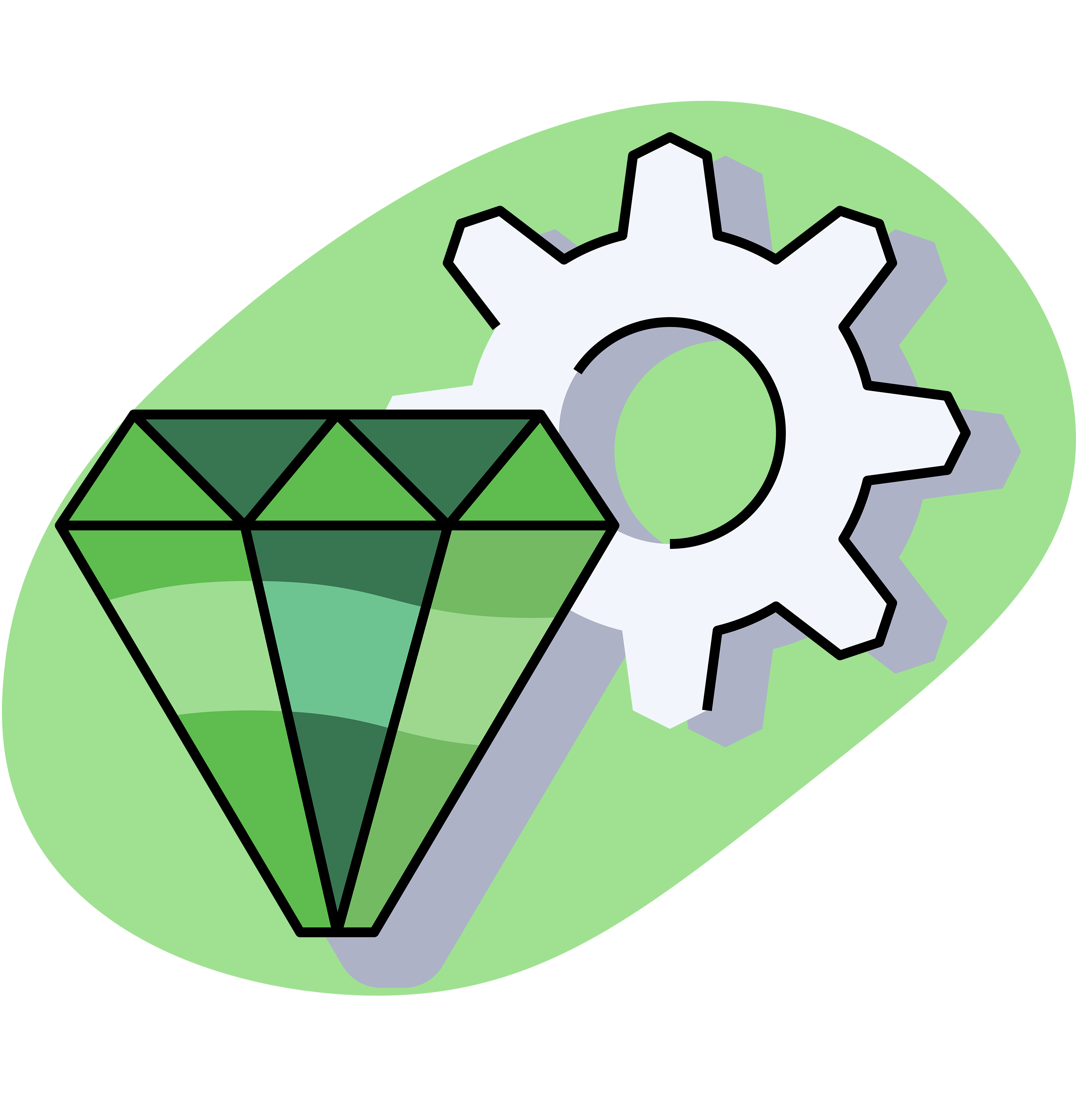
Technologies
Our modelling and simulation technologies extend from the component level to the system level.
Our system-level approach is completely independent of the physical domain, so that it is possible to deal in a unitary way – i.e. with a single software platform – models that cover different sectors (mechanical, thermal, thermal -hydraulic, hydraulic, pneumatic, electrical, control). This can be of vital importance for innovative applications, such as the integrated plant study (which combines very different subsystems), or the development of sophisticated components.
For applications that require very detailed and verticalised models on the single component, we can also use the latest generation platforms for CFD, FEM and other calculation tools
Solutions
Our modelling and simulation solutions cover a wide spectrum of application sectors and types of study, and are strongly connected with the methodologies and disciplines of control systems. Our offer can be summasized in the following macro-areas:
- General-purpose models, aligned with industrial standards and suitable for system-level studies, such as the
verification of the dynamic behaviour of a plant, the guidelines for equipment sizing, the optimised design of
production plants and logistics; - Detailed models, interchangeable (where possible and if appropriate) with those at system level, for studies aimed
at evaluating the behaviour of one or more individual components; - Modelling libraries for specific technological sectors. Discover the libraries.
With our solutions, it is possible to simulate each part of the system with the right degree of detail with respect to the problem under analysis, and to produce results in the form that best meets the standards of the customer and of the end user.
The Dynamica team can provide full support to make the best use of our solutions throughout the project workflow.
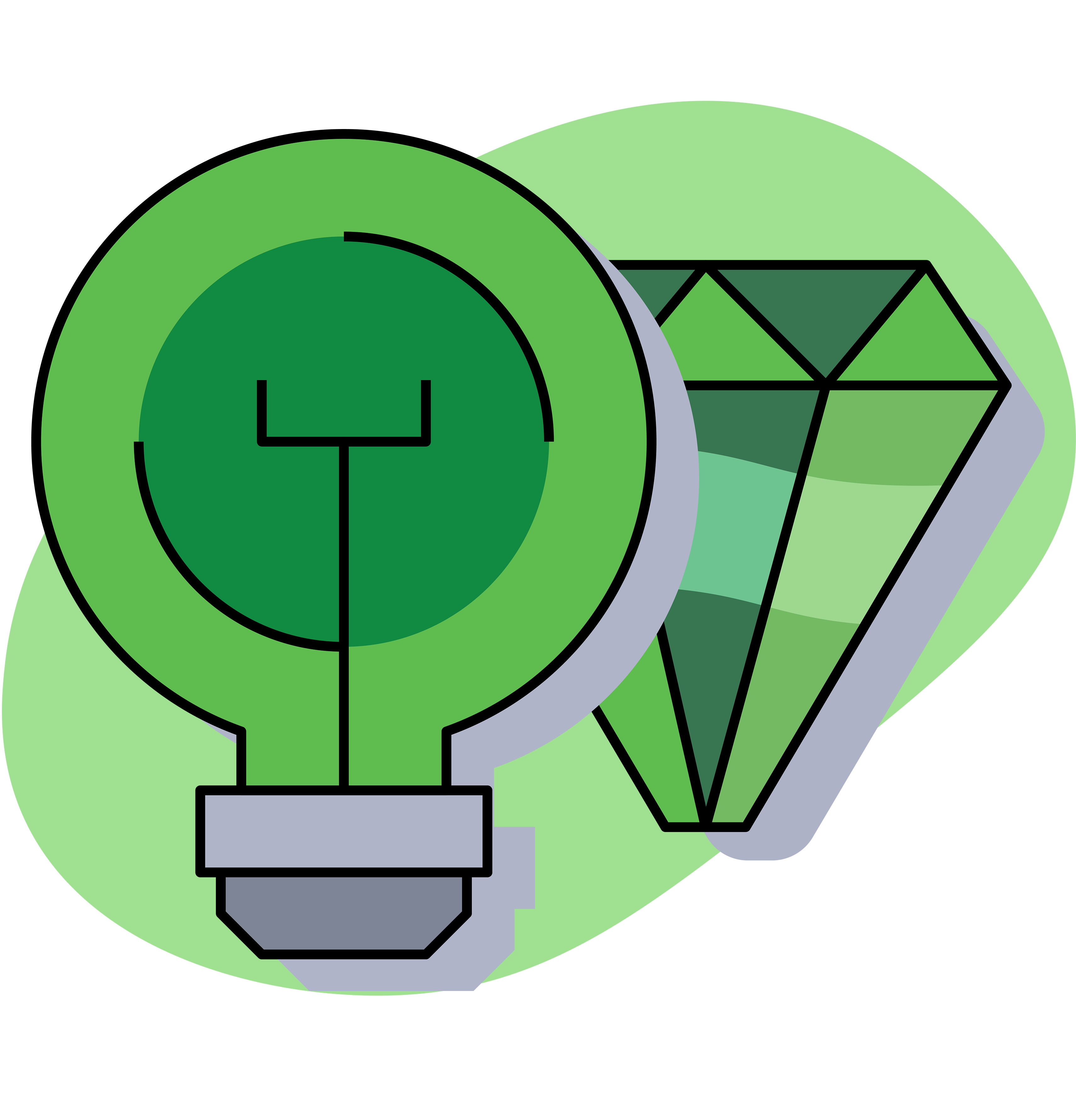
Any Idea or Project you wish develop with us?
info@dynamica-it.com